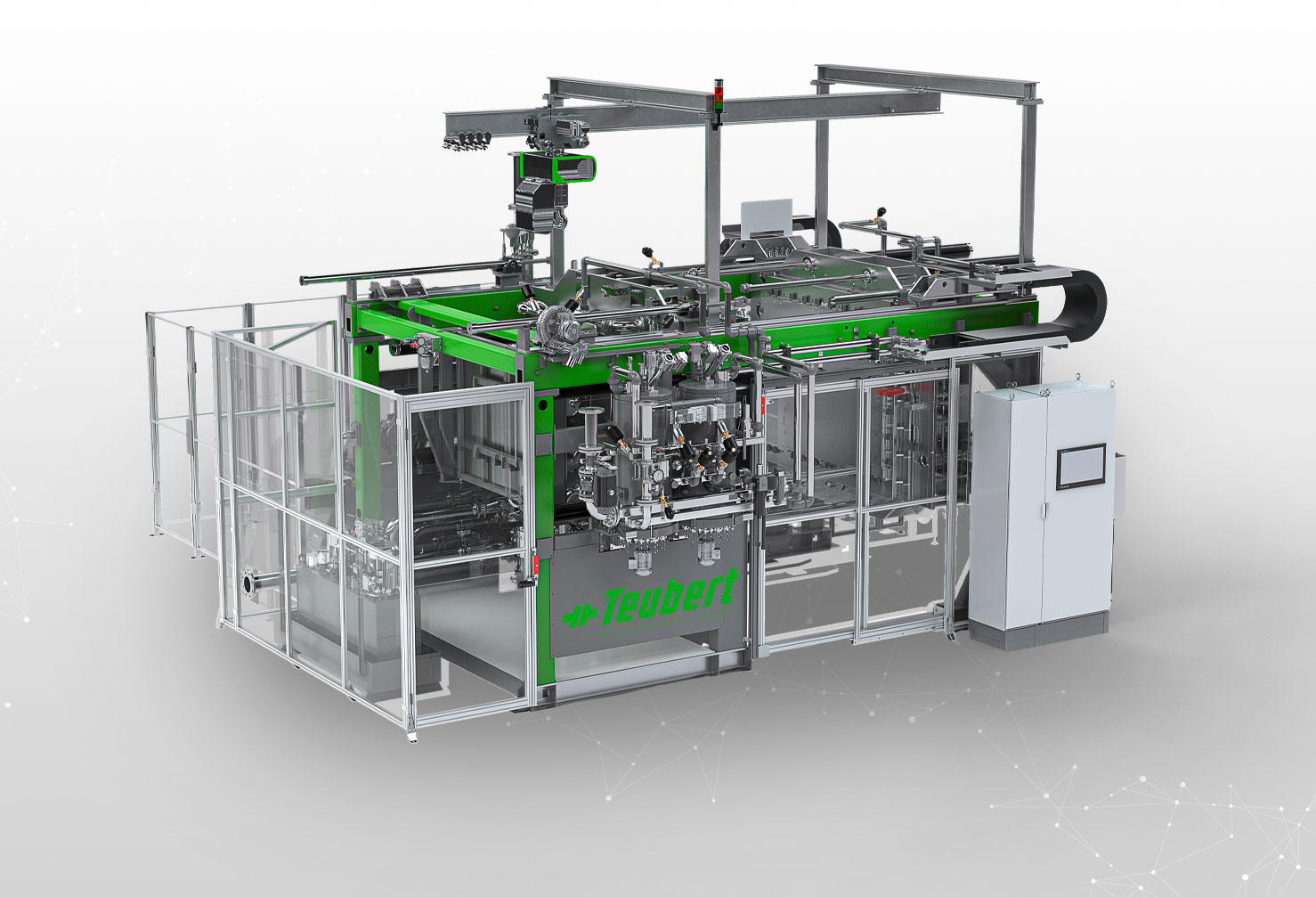
Formteile aus EPP – individuell und innovativ
Als „der Schaum, aus dem die Träume sind“ wird Partikelschaum wie expandiertes Polypropylen oft in den Medien bezeichnet. Der Grund: Mit multifunktionalen Materialeigenschaften und Designfreiheit bis ins Detail ermöglichen die kleinen Kügelchen aus EPP über einen anwendungsorientiert durchgeführten Formteilprozess den Weg zum Wunschprodukt.
Bei der Formgebung des schadstofffreien Werkstoff-Granulats wird zwischen den klassischen dampfbasierten und den neuartigen dampflosen Verarbeitungstechnologien differenziert. Für alle Verfahren gilt, dass je nach Anwenderbedürfnis ein Formteildichtebereich zwischen 20 und mehr als 200 kg/m³ realisiert werden kann. Und, besonders wichtig für unsere Umwelt: Die Verarbeitung von EPP erfolgt ohne klimaschädliche Treibmittel!
Dampfbasiertes Verarbeitungsverfahren
Die Herstellung von EPP-Formteilen erfolgt seit der Markteinführung von expandiertem Polypropylen durch das Verschweißen der EPP-Schaumperlen mittels Heißwasserdampf. Der Wasserdampf, als Energieträger eingesetzt, sorgt für das Erwärmen, Anschmelzen und Verschweißen der losen EPP-Partikelschaumperlen im Inneren der Werkzeugkavität.
Im ersten Prozessschritt fährt die bewegliche Werkzeughälfte (meist elektrisch) zu. Anschließend wird durch das Aufbringen einer Schließkraft mittels hydraulischen Spannzangen die Kavität geschlossen.
Der zweite Schritt zeigt die Befüllung der Kavität mit EPP-Partikeln. Hierbei gelangen die Partikel mittels Druckluft über die Füllinjektoren in die Werkzeugkavität. Der Befüllvorgang kann durch zwei unterschiedliche Verfahren erfolgen:
Tauchkanten- bzw. Crackspalt-Verfahren:
Beim Crackspalt-Verfahren wird das Werkzeug beim Füllvorgang nicht komplett geschlossen. Die Schaumpartikel werden somit fast drucklos in die Werkzeugkavität eingeführt und anschließend durch Schließen des Werkzeuges mechanisch verdichtet. Werkzeugseitig ist für diese Verfahrensvariante eine sogenannte Tauchkante erforderlich. Das Crackspalt-Verfahren eignet sich besonders zur Herstellung von sehr dünnen Formteilen mit höheren Materialdichten.
Kompressions- bzw. Druckfüll-Verfahren:
Die Befüllung nach der Kompressionsmethode basiert auf einem Druckgefälle zwischen Druckfüllanlage und Werkzeug. Mittels Luftstrom werden die Partikel über Füllinjektoren in die Kavität des Werkzeuges geblasen. Durch den aufgebauten Überdruck, den sogenannten Staudruck, werden die Schaumperlen verdichtet. Mit zunehmendem Staudruck werden die Schaumperlen stärker komprimiert, das heißt, es können mehr Perlen in eine Kavität gefüllt werden. Somit führt ein höherer Staudruck auch zu einer zunehmenden Bauteildichte. Je nach verwendetem Materialtyp wird der Staudruck individuell eingestellt und liegt üblicherweise zwischen 0,8 und 4,0 bar.
Der dritte Prozessschritt beinhaltet das Bedampfen der komprimierten EPP-Perlen. Dabei erfolgt die Temperaturführung über den Dampfdruck. Für die Verarbeitung der EPP-Schaumperlen ist in Abhängigkeit des Rohmaterials und der gewünschten Formteildichte eine Temperatur zwischen 140 und 160 °C erforderlich, die bei einem Dampfdruck zwischen 2,5 und 4 bar erreicht wird. Je nach Prozessführung kann zwischen der Querbedampfung und der Autoklavbedampfung differenziert werden. Bei der Standardprozessführung erfolgt zunächst die Querbedampfung. Realisiert wird dieses Verfahren durch geöffnetes Dampfventil und geschlossenes Kondensatventil auf einer der beiden Werkzeughälften bei gleichzeitig entgegengesetzter Schaltung auf der gegenüberliegenden Seite. Somit durchströmt der Dampf insbesondere das Innere der Werkzeugkavität, was eine homogene Versinterung der Partikel im Bauteilinneren gewährleisten soll. Um eine vollständige Verschweißung garantieren zu können, erfolgt üblicherweise nach der Querbedampfung eine Autoklavbedampfung. In diesem Prozessschritt strömt der Dampf von einer Seite durch die Partikelfüllung, wobei auf der gegenüberliegenden Seite die Kondensatventile geschlossen sind. Diese Methode der Bedampfung sorgt zum einen für eine Ablösung des Formteils von der Werkzeugwand, was sich positiv auf die Entformung auswirkt, zum anderen für eine homogene Verschweißung auf der Bauteiloberfläche.
Mittels aktiver Kühlung, üblicherweise durch Sprühkühlung mit Wasser, wird das Formteil, das nach dem Bedampfungsprozess in etwa eine Temperatur von ca. 140 °C besitzt, auf ca. 80 °C abgekühlt. Das Kühlprinzip beruht hauptsächlich auf einer Verdampfungskühlung. Dabei entzieht das Wasser dem Formteil indirekt über das Werkzeug die Wärme. Dieser Schritt sorgt für die nötige Stabilisierung der Schaumstruktur und bietet im Anschluss die Möglichkeit der Entformung.
Beim Öffnen der Form wird das Formteil mit pneumatisch gesteuertem Auswerfen aus der Haube gedrückt. Zusätzlich kann das Entformen durch einen Luftstoß aus den Dampfdüsen unterstützt werden.
Detailliertere wissenschaftliche Betrachtungen, die beim dampfbasierten Formschäumen von EPP auftreten, finden Sie in folgender Publikation.
Strahlungsbasiertes Formschäumen
Bei der strahlungsbasierten EPP-Verarbeitung mit der Radiofrequenz-Technologie (RF-Prozess) erfolgt der Energieeintrag in die EPP-Partikelschaumperlen mittels Radiowellen mit einer Frequenz von 27,12 MHz, was einer Wellenlänge von ca. 11 m entspricht. Ein Hochfrequenzgenerator erzeugt ein elektromagnetisches Wechselfeld, wodurch sich die Dipole des in der Form befindlichen Materials innerhalb des Feldes ausrichten. Die so erzeugten Molekülschwingungen führen zu einer Erwärmung und Erweichung der Schaumperlen, wodurch diese unter dem Forminnendruck verschweißen.
Der RF-Prozess ermöglicht den Verzicht auf die für den Dampfprozess notwendige Peripherie zur Dampferzeugung. Dadurch wird eine dezentrale Produktion möglich. Ein weiterer Vorteil der RF-Technologie ist das enorme Energieeinsparpotenzial, da die Radiowellen direkt ins Material einkoppeln und ein Aufheizen und Abkühlen der Form selbst entfällt. Das begünstigt einen weit höheren Wirkungsgrad. Die Erwärmung im Inneren kann darüber hinaus einen positiven Einfluss auf den Verschweißungsgrad und, damit einhergehend, auf die Festigkeit der Formteile nehmen. Bei gleichen mechanischen Eigenschaften kann so, zum Beispiel durch Wanddickenreduktion, Material eingespart werden.
Dampfloses Formschäumen mittels ATECARMA®-Verfahren
Das ATECARMA-Verfahren kann Partikelschäume effizient, dampf- und wasserfrei zu Formteilen verarbeiten. Die innovative und ressourcenschonende Herstellung von Hybridbauteilen in nur einem einzigen Arbeitsgang ermöglicht bisher nicht realisierbare Produktentwicklungen, zum Beispiel das Ausschäumen von komplett geschlossenen Hohlstrukturen.
Beim ATECARMA-Verfahren werden die Partikelschaumperlen vor der Verarbeitung mit einem passenden, schadstofffreien Aktivator benetzt und getrocknet. Hierbei wird die Oberfläche der Schaumstoffperlen funktionalisiert. Bei der Bauteilherstellung werden die vorbehandelten Perlen in ein formgebendes Werkzeug gefüllt. Durch Energieeintrag in das Formwerkzeug kommt es zu einer chemischen Reaktion des Aktivators. Dabei werden sowohl die Schaumstoffpartikel untereinander als auch ggf. weitere in der Form befindliche Verbundmaterialien und Einleger mit dem Schaumstoff verbunden und das fertige Formteil entsteht.