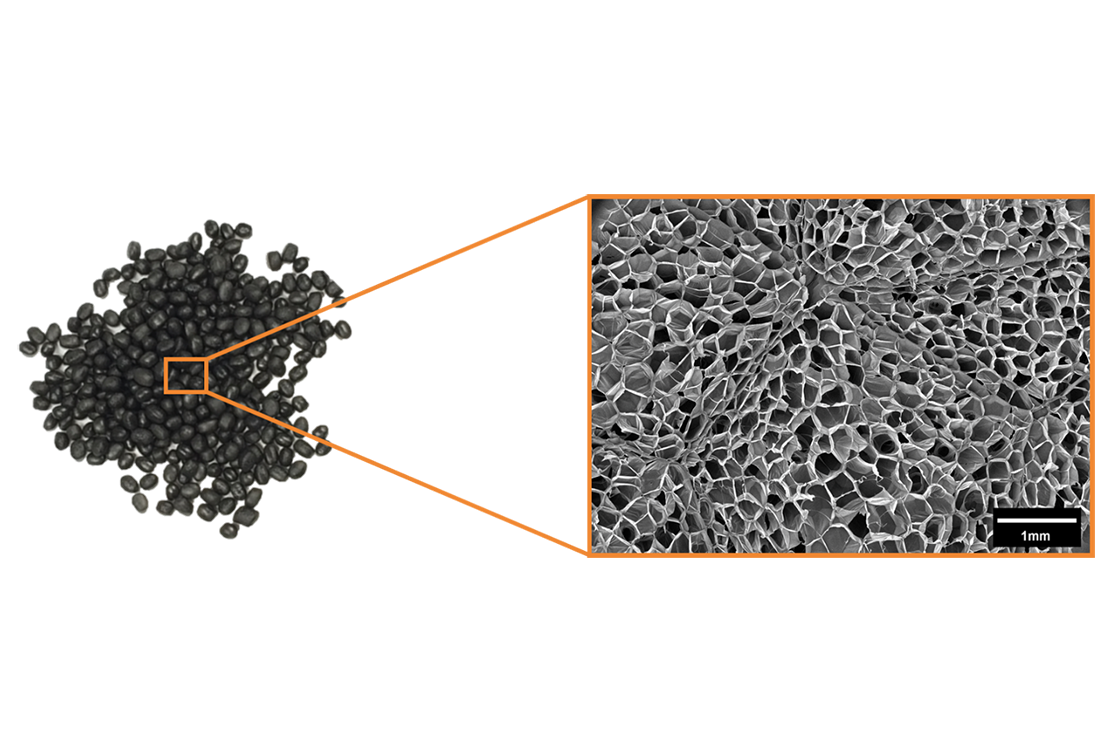
Production of EPP as a raw material: from polypropylene granules to beads
Expanded polypropylene (EPP) is a recyclable particle foam that is already pre-foamed into foam beads by the raw material manufacturer. During the production of foam beads by the individual EPP manufacturers, we can distinguish between two different methods and therefore two grades of expanded polypropylene: autoclave and extruded EPP foam.
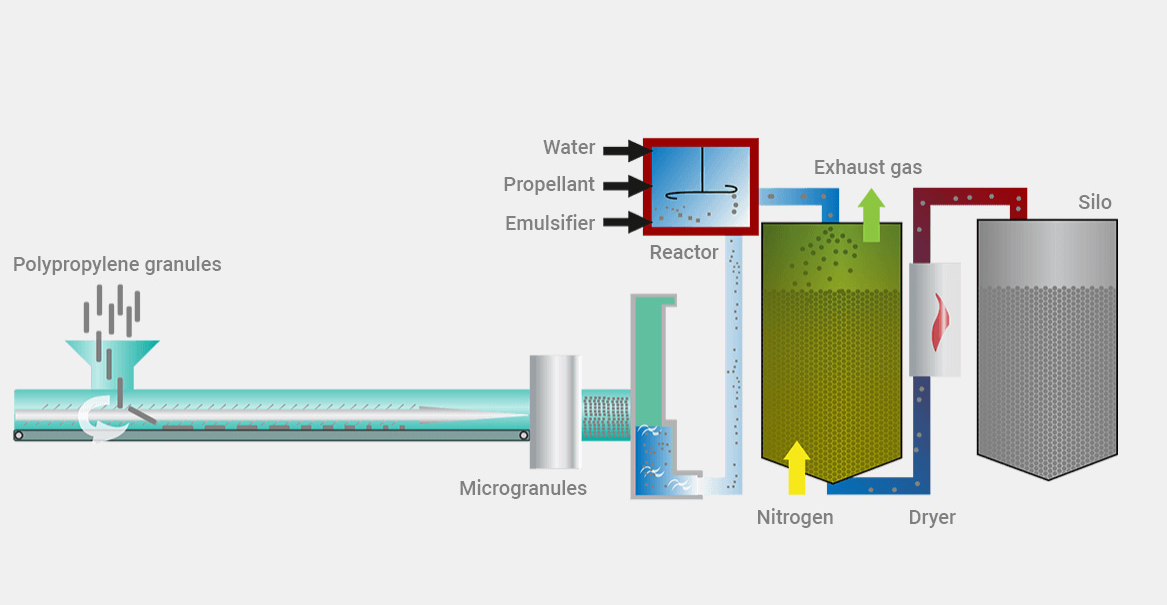
Autoclave EPP foam
In the autoclave process, polypropylene microgranules are filled into a reactor (autoclave) together with a mixture of hydrocarbon (usually isobutane, which evaporates easily) and water. To ensure the individual substances mix well, an emulsifier is also used. The closed system is then pressurised to approx. 30 bar and heated to a temperature of about 100°C with constant stirring. During this process, which takes several hours, the hydrocarbon gas diffuses into the microgranules. After a resting time of several hours in the reactor, the mixture is transferred to the retractable container. This container contains a nitrogen atmosphere under normal pressure. Due to the pressure difference between the reactor and the retractable container, and therefore the prevailing overpressure inside the particles, the foaming agent expands and the granules inflate. Next, the EPP foam beads are dried and then stored in a silo for further processing.
Autoclave EPP foam often has better energy absorption values, but is usually only offered in gray and white as standard.

Extruded EPP foam
During the production of EPP foam particles using the extrusion process, the foaming agent is already added to the polymer melt in the extruder. PP copolymers, mostly polypropylene-ethylene block copolymers, are used as the base polymer. Similar to the traditional foam extrusion process, the PP copolymer is melted in the extruder under high pressure and then homogenised with the foaming agent flowing into the polymer melt until a single-phase polymer-gas mixture is formed. Halogen-free, saturated hydrocarbons (especially propane) are used as foaming agents. The melt strands formed when the mixture exits through a perforated nozzle expand due to the abrupt drop in pressure and are formed into bead shapes using a rotating blade in the underwater pelletiser. After being dried, the foam particles are transported to silos and are ready for further processing. Extruded EPP foam is easier to produce in different colours and is more temperature resistant. However, higher vapour pressures may be required for moulding.
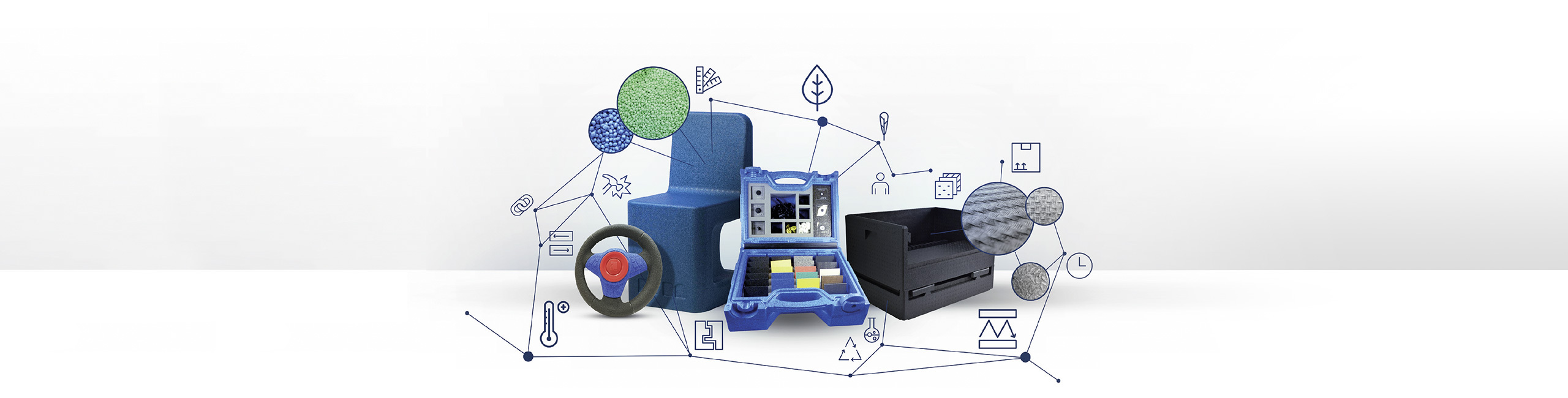
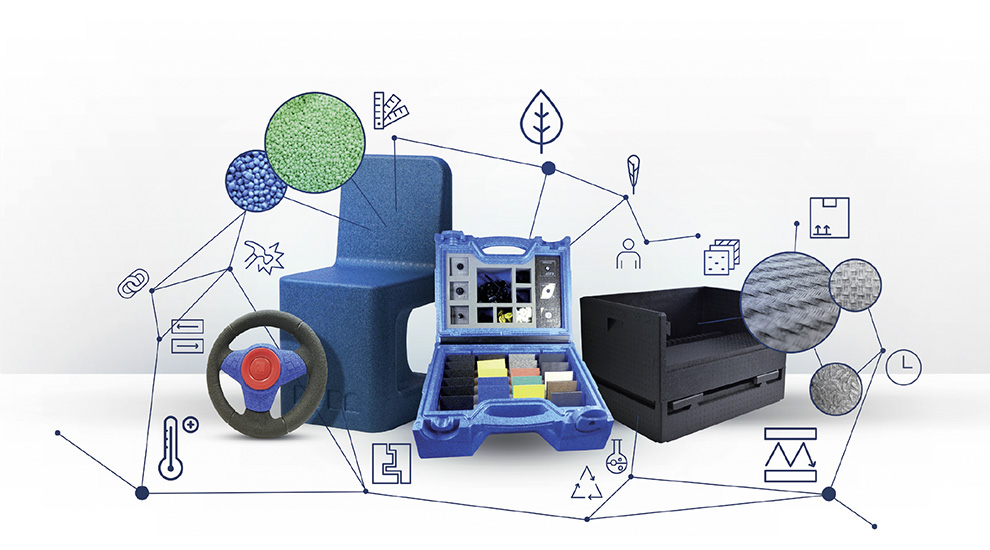
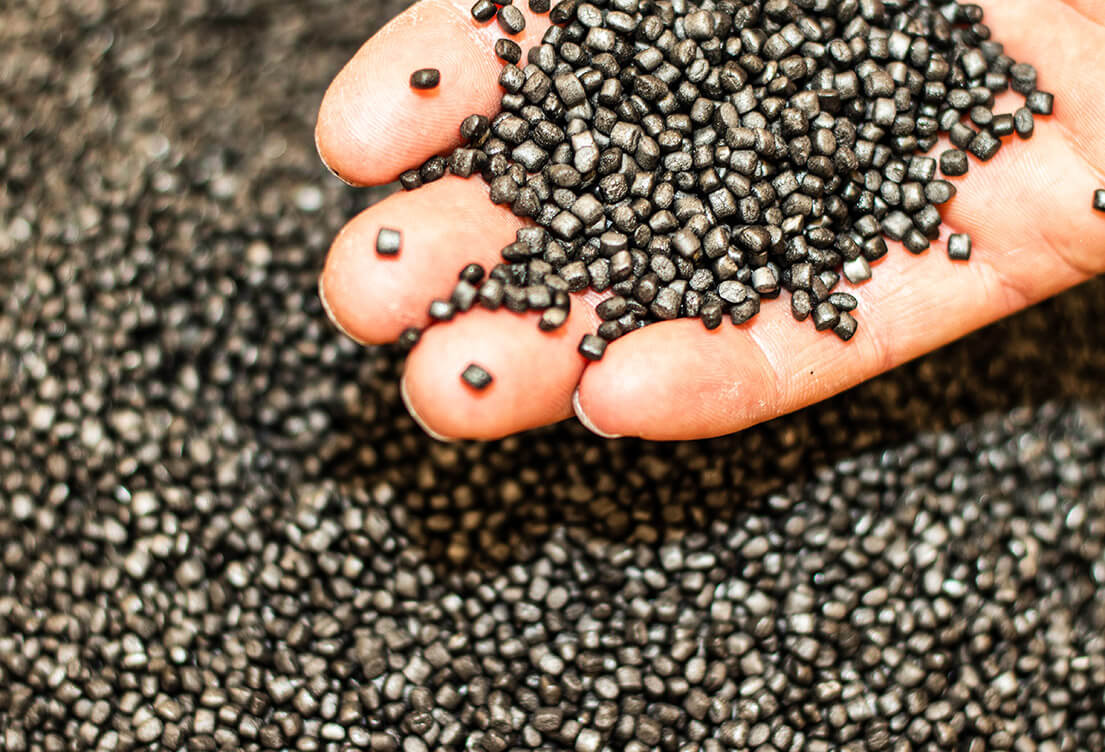
EPP foam beads – highly versatile
No matter what method is used in the production of the raw material: The result is environmentally friendly, recyclable and versatile foam beads made from EPP.
In some cases, the EPP granules do not need to be further processed into moulded parts, as the pressure-absorbing, comfortable particle foam beads are ideal as a filling for relaxation pillows, breastfeeding pillows and beanbags, medical living aids and lounge furniture.