
The life cycle of EPP products
A material that can be processed in an energy-efficient manner, can be shaped and designed with virtually no limits, and which offers extreme resistance – expanded polypropylene is a sustainable solution, suited to use in a wide range of industries.
An important aspect of the sustainability concept is to avoid waste. Not just packaging waste, but also waste that arises due to poor storage and inadequate transport packaging. Reusable transport packaging made of EPP is therefore primarily used in the food sector due to its outstanding thermal insulation properties. But EPP also performs perfectly when used to transport sensitive products in the medical and pharmaceutical industries.
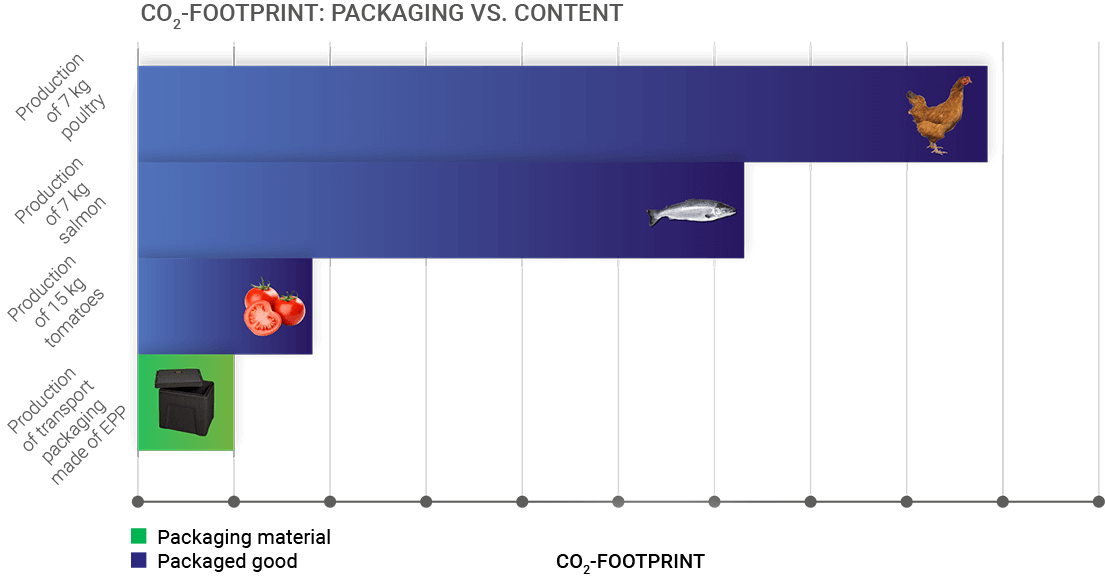
The use of EPP boxes in the food industry
Today’s food industry has a big problem: Before being placed on display by the retailers, the industry loses up to 14 per cent of its goods. Due to unfavourable storage conditions and inadequate transport packaging, a significant proportion of the goods are damaged or spoiled. This leads to an immense waste of resources, because the ecological footprint of the packaged goods is usually significantly larger than that of the packaging material.
To avoid the waste of resources caused by food spoiling in transit, safe transport packaging is needed – sturdy and preferably reusable. This is where EPP comes into play. Reusable transport packaging made of expanded polypropylene:
- has very good insulating properties and protects perishable and sensitive goods in particular, both during transport and storage.
- can be stacked well. The EPP boxes can easily be stowed in the transporter as well as in the storage room to save space.
- A reusable and thus sustainable solution.
- Food-safe and free from harmful substances.
- are extremely light and guarantee a low transport weight.
- easy to clean and can therefore be reused several times.
Use of EPP as packaging and transport material
Reusable transport packaging made of expanded polypropylene is not only used in the food industry. Packaging material made of EPP plastic is also suitable for other industries which require goods to be transported safely. Transport boxes made of expanded polypropylene are extremely shock-absorbent and therefore also protect sensitive parts, such as pharmaceutical and medical products. The boxes are reusable and can be kept in circulation for several years. After this time they can be recycled easily.
Use of EPP in the automotive industry
As one of the most important economic sectors, the automotive industry is one in which EPP will become increasingly relevant in the future. The innovative material can be used in a wide range of components: From the bumper, to the rear window shelf, to the sun visor. By using components made of expanded polypropylene, a lot of weight can be saved in vehicle construction, which leads to less fuel consumption and therefore to a reduction in the CO2 emissions. Vehicle safety also benefits from the positive properties of the foam: Due to its high energy absorption capacity, EPP is particularly appreciated in the area of shock absorption. Furthermore, the promising foam is also relevant for the field of electromobility and is used, among other things, as a thermal insulating material in doors.
Component logistics in this industry also makes use of the durability of EPP: Load carriers in which components are delivered to the assembly line can be reused continuously for up to 7 years.
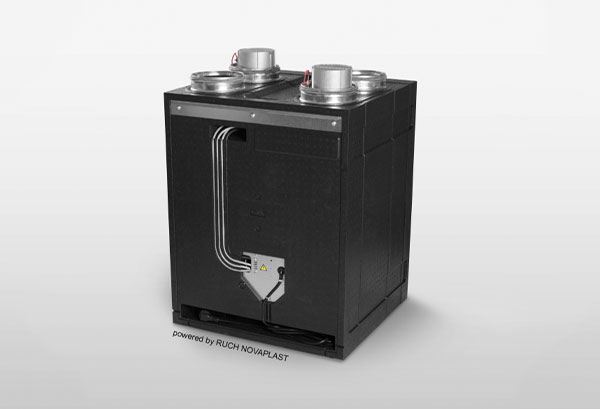
Using EPP for technical moulded parts
The possible areas of application for expanded polypropylene are almost unlimited. In the areas of heating, ventilation and air conditioning technology, technical moulded parts made of EPP are the preferred choice. The reasons are obvious: EPP is extremely light and resistant, which in turn guarantees a long service life. Technical moulded parts can be produced individually and precisely from expanded polypropylene. And no waste is produced in the process, as would be the case with machining. What’s more, EPP plastic has great insulating properties and therefore ensures low heat loss. This leads to a noticeable energy saving, from which both the customer and the environment benefit.